The SPM-SLIM riveting system allows the objectification and control of rivet fastening.
The system is able to verify the correct force and stroke, count the number of operations that make up the assembly cycle, connect to a PLC and execute the data transfer to a system.
The SPM-SLIM riveting system allows the objectification and control of rivet fastening.
The system is able to verify the correct force and stroke, count the number of operations that make up the assembly cycle, connect to a PLC and execute the data transfer to a system.
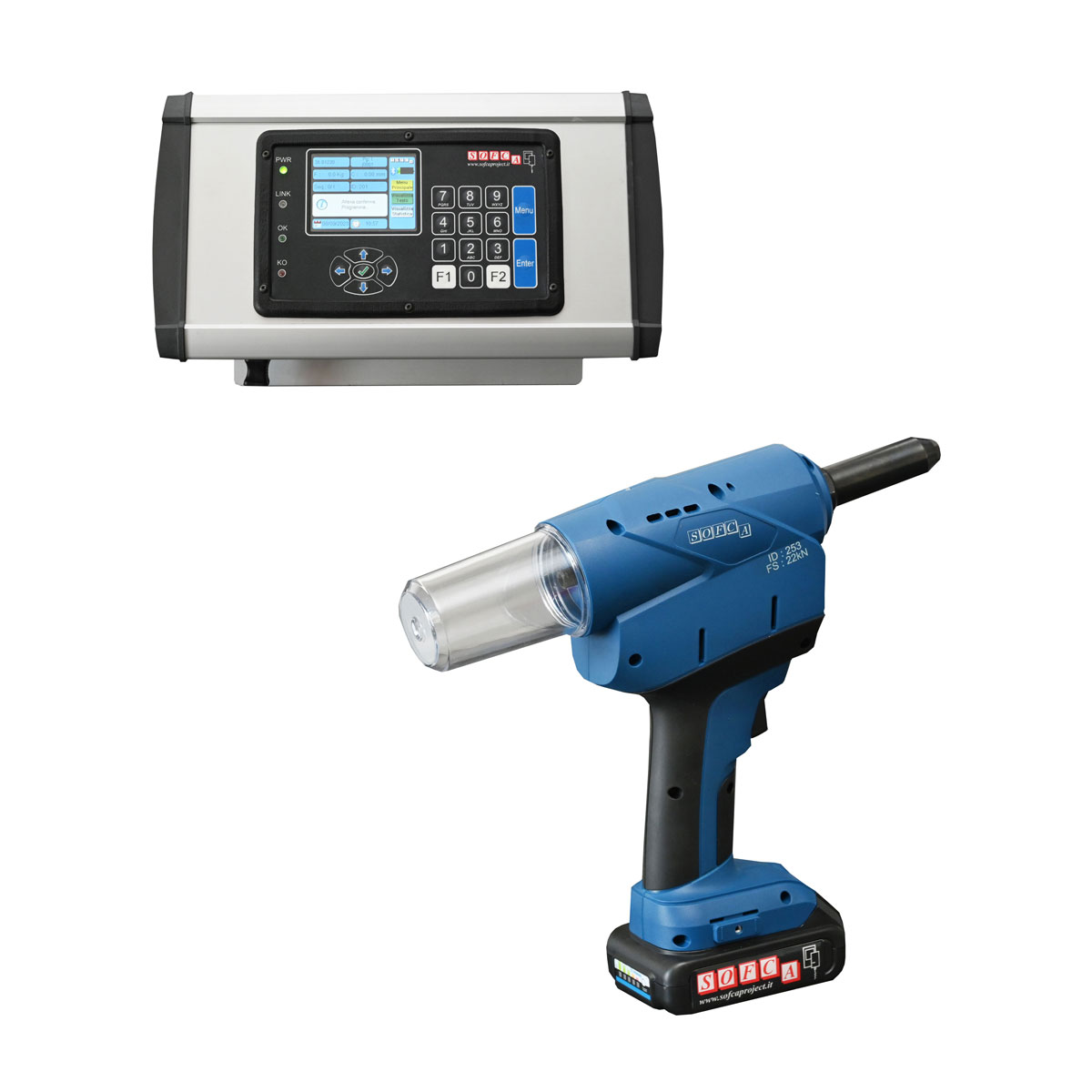
During programming an expert performs a sequence of assemblies that have to be performed properly; in this phase the equipment is set in acquisition mode with the purpose of learning what is being done. In the next phase of execution the equipment will have to monitor the operations on the production line, verify them with respect to what it has learned previously and, in case, report any anomaly in the values of the measured parameters.
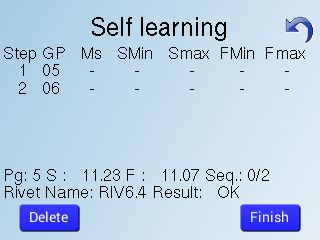
Self-learning screen
The certainty that this force is actually the one due, will be guaranteed by the RIVETING system, which will or will not validate the correct tightenings of the clamp based on the parameters set by self-learning; after which, in production, the system is able to check the correct tightening, count the number of rivets that make up the assembly cycle, connect to a PLC.
For the control and monitoring of the tightening, the control unit is a versatile tool that can work independently or cooperatively with external devices such as the PLC, the program selection device or the Barcode and interface with the systems used by large companies of the automotive field.
The control unit uses the Bluetooth connection to exchange data with the tool.
The use of the Bluetooth system offers the advantage of eliminating the wiring for the transfer of information between the tool and the control system when the tool is used at a distance of no more than 15 meters from the control unit. The use of a system with Bluetooth technology allows the operator to be autonomous in the handling of the tool during the tightening operations.
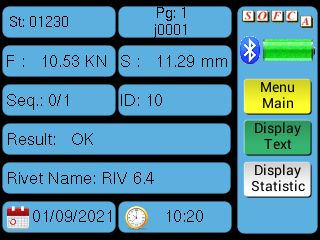
Main screen
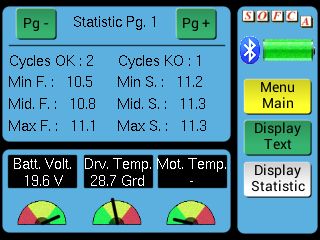
Statistics screen
The peculiarity of the RIVETING system lies in a better guarantee of the rivet tightness by applying the following strategies:
- Self-learning for setting the parameters that ensure a good tightening of the rivet
- Detection, during the tightening and in real time, of the values of these parameters by reading the sensors and release of data on an external PLC
- Scheduled maintenance to be carried out by the control unit which, based on the implemented cycles, will warn the operator
Characteristics of the RIVETING system:
- Practical system, since there are no cables and hoses to drag
- Tool weight, about 2 kg
- Maintenance limited to the replacement of the consumable
- Long autonomy of the battery, on average it lasts about 8 hours
- Battery replacement in about 4-5 seconds
- About one hour time to charge the 20 VDC lithium battery with the convenience of having the second battery in charge
- Graph of Force/Stroke with indications of their acceptability thresholds after cycle performed
- PLC interface
- Availability of an on-site bench for the verification of the tightening force through the use of a load cell with ACCREDIA reference
Features of the riveting tools
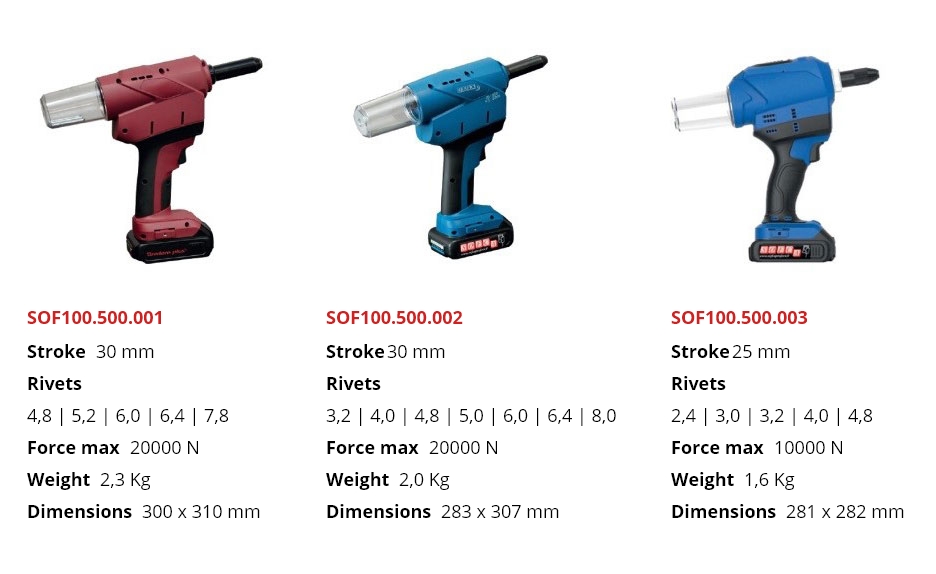
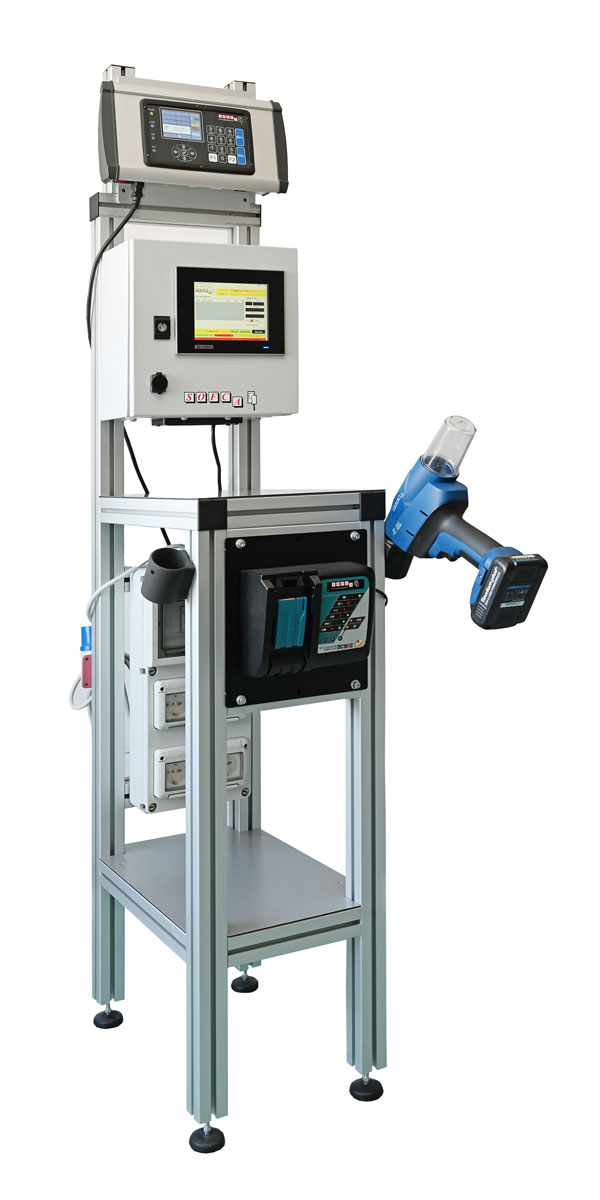
Example of a SPM SLIM – RIVETING configuration
The following figure shows a possible SPM-SLIM - RIVETING bench, in one of its typical configurations:
- Control Unit SPM SLIM – RIVETING
- Dedicated printer for timely report of the operations
- Barcode device to select the appropriate program
- Riveting tool with beacon information
- Customizable bench with anodized aluminum frame
- GP BOX unit for the selection of the riveting program